Polyurethane Material Introduction and Industry Insight
Polyurethane, commonly referred to as PU, is a versatile polymer utilized across various industries and applications. Its different formulations and production processes allow polyurethane to take on multiple forms, such as foam or elastomer. The production of polyurethane is complex and requires a thorough understanding of chemistry. This article will focus on three essential aspects of polyurethane production.
First, we will cover the manufacturing process of polyurethane, divided into three sections: the production of isocyanates, the creation of polyols, and the production of polyurethanes. Second, we will discuss the significant applications of PU materials, including PU coatings and adhesives, PU foams, and PU sealants and elastomers.
Raw Materials and Formation of Polyurethane
In 1937, Otto Bayer and his colleagues discovered polyurethane while working on the production of polyurea from aliphatic diisocyanate and diamine. They made this discovery at the laboratories of I.G. Farben in Leverkusen, Germany, forming PU from aliphatic diisocyanate and glycol. While the study of PU formation and production continued, it became commercially available only fifteen years later.
The process of PU production involves an exothermic reaction between a mixture of alcohol and multiple hydroxyl (-OH) group molecules with isocyanates. These molecule groups can be diols, triols, or polyols, while the isocyanates should be multiple isocyanate groups (-NCO), such as diisocyanates or polyisocyanates.
Industries consider TDI (toluene diisocyanate) and MDI (methylene diphenyldiisocyanate) as the most widely used and critical forms of aromatic polyisocyanates. The production of MDI and TDI involves a highly poisonous chemical compound, phosgene, making the industry concentrated and oligopolistic in nature, with top manufacturers controlling a significant portion of the market share. Consequently, the pricing and stock of isocyanates heavily depend on these top chemical manufacturers. Additionally, growing environmental concerns and volatile raw material prices pose challenges for polyurethane manufacturers. MDI and TDI have witnessed price swings due to fluctuations in their precursor markets, such as petrochemicals.
The second part of PU manufacturing involves the production of polyols, which make up at least 90% of the total fabrication of PU. These polyols can be hydroxyl-terminated polyethers or hydroxyl-terminated polyesters. The reaction of these compounds with isocyanates produces PU with specific properties. The degree of molecular cross-linking, influenced by the molecular structure, size, and flexibility of the chosen polyols, determines the mechanical properties of the polymer. Reactions with biopolymers, such as soybean oil and epoxypropane, have shown that polymers can be derived from renewable sources.
The production of polyurethanes involves forming a linear polymer from the reaction of two hydroxyl groups with either TDI or MDI. Polyols containing multiple hydroxyl groups react, leading to the intertwining of long-chain molecules at their intermediate points, creating a stiffer polymer structure with enhanced mechanical features, resulting in rigid PU. The PU undergoes various chemical reactions to control the formation process and achieve specific properties. Different additives serve different purposes in PU manufacturing. For example, catalysts speed up the reaction process between the polyols and polyisocyanates, while smoke suppressants reduce smoke generation when burning PU. One of the most popular uses of PU materials is as blowing agents and surfactants, creating PU foam to control bubble formation and produce cell structure foam. Cross-linking of molecular strands modifies the PU structure, enhancing reinforcement and increasing functionality.
Applications of Polyurethane
A significant portion of polyurethane is produced as foam, often in large blocks that are later cut into smaller pieces. PU foams are primarily used as cushions or for thermal insulation. The rigidity or flexibility of PU depends on its specific density levels, which also determine its application. For example, low-density, high-flexibility PU is ideal for cushioning due to its high resistance to fatigue. Polyurethane foam is widely used in interior components and lightweight automotive parts to promote fuel and energy savings. PU is also an excellent insulation material for electrical equipment due to its oil resistance. The density of PU can be increased during manufacturing to make durable cables. Additionally, PU's high flexibility and biostability make it suitable for artificial heart valves, ensuring they can expand and contract like natural valves.
Another advantage of polyurethane is the ease of starting the PU process at different levels due to the low molecular weight of the pre-polymer liquid, making it easy to handle. The pressure of the starting materials is also relatively low. The polymerization process can convert initial monomers and pre-polymers into solid end products at various stages of the reactions. The inherent properties of rigid and flexible foams, such as structural stability, enable the production of thermally insulating products. PU's adhesive properties ensure building panels offer sufficient strength and longevity. Efficient and insulative foams are used in 'green' buildings and sustainable infrastructure projects to lower energy costs in developed regions like Europe and North America. Due to its high durability, abrasion resistance, and flexible physical properties, PU is also an excellent material for shoe soles.
Polyurethane coatings are essential for vehicles, walls, floors, cables, bridges, and textiles, among other applications. The global coating market generates approximately 2 billion USD in sales, reflecting high demand for PU-coated finished goods in industrial and architectural industries. The development of environmentally friendly coatings with polyaspartic and 2K waterborne PU technology has opened new avenues for sales growth. PU's properties, such as durability, corrosion resistance, and weather resistance, make it suitable for coatings. Coatings protect surfaces from pollution or corrosion and enhance their appearance. For example, vehicle coatings ensure a glossy exterior to protect against corrosion or scratching while improving color retention. Japan records high consumption of PU coatings, likely due to its numerous automotive assemblies and architectural companies.
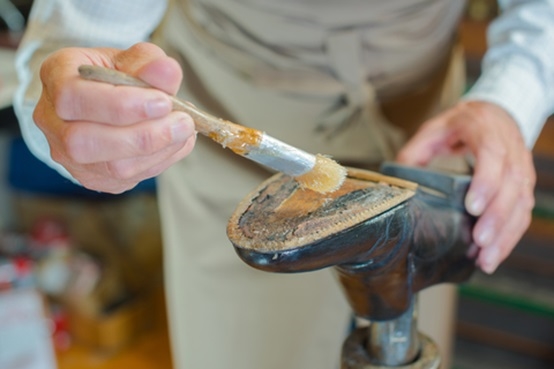
PU also serves as an adhesive or binder, offering a high property profile compared to other natural adhesives. Its versatility allows for the production of glues with high shear and tensile strength. Industries such as textiles, furniture, footwear, construction, and packaging heavily rely on
PU adhesives. PU adhesives' high resilience and strength ensure long-lasting bonds. PU adhesive qualities also facilitate recycling end-of-use vehicle tires into surfaces like sports tracks, preserving natural resources. For example, fiberboard is a product of
PU binders combined with woodchips. Additionally,
solvent-borne PU adhesives are becoming less popular, with industries shifting to
waterborne PU materials in compliance with VOC (volatile organic compounds) guidelines, promoting solvent-free and environmentally friendly options.
Sealants attach two surfaces by filling the space between them, with significant demand from construction, consumer products, transportation, aerospace, and electronics industries. The construction industry leads in demand for
PU sealants, followed by transportation and industrial markets. PU sealants are vital in manufacturing materials that require high-strength, water-resistant seals. PU's properties ensure materials recover easily after bending or pulling without losing shape.
PU elastomers are rubber-like polymers that can stretch significantly and return to their original shape once the stretching force is removed, similar to a spring. Elastomers resist flow when distorted by external forces. PU elastomers' versatility allows them to attain optimal physical properties for specific applications. They are customizable for various market segments and can perform multiple functions for metals and ceramics due to the dependability of cast elastomers. In rubber form, cast elastomers offer high resiliency and flexibility. PU elastomers have diverse applications and a wide range of hardness and processing features. They exhibit high resistance to substances like oil, petrol, and non-polar solvents. Only a few compounds, such as oxidizing agents and strong basic and acidic elements, affect completely cured cast elastomers. Popular cast elastomer products include skateboard wheels,
forklift tires, and press-on tires. PU elastomers can outwear metals, plastics, and rubbers simultaneously. However, using polyester polyols in current PU system technologies reduces the hydrolytic stability of PU elastomers, limiting their applications.
Many companies are investing in innovative research to meet the increasing demand for high-performance PU spray elastomers and cast applications. The primary focus is on enhancing abrasion resistance, a crucial physical and mechanical property for wear applications like coating or technical casting items. Improved PU elastomer technology includes developing PU elastomers with intrinsic self-healing properties, contributing to segment growth. PU elastomers are expected to become the fastest-growing PU product, offering combined benefits of plastics and rubbers for high flexibility and impact and shock resistance in high-performance applications.
Conclusion
The polyurethane industry can be segmented by product into foams, coatings, adhesives, sealants, elastomers, and other products. The polyurethane market size was around 50 billion USD in 2015 and is projected to grow steadily due to increasing demand for lightweight and durable materials for furniture, construction, electronics, appliances, automotive, footwear, and packaging. It is essential to research PU materials with faster and less costly production processes, stronger properties, and more environmentally friendly options.
TPUCO Polyurethane Products:
https://www.taiwanpu.com/en/product/